1.MIM is a metal forming process
MIM (Metal injection Molding) is the abbreviation of metal injection molding. A method of forming a mixture of metal powder and binder into the model. It mixes the selected powder with the binder first, and then mixes the mixture to form the shape needed for injection molding.
2 、 MIM process steps
The MIM process combines the flexibility of injection molding design and the high strength and integrity of precision metals to achieve low cost solutions for extremely complex geometric components. MIM process is divided into four unique processing steps (mixing, molding, degreasing and sintering) to achieve the production of components, and the product characteristics determine whether surface treatment is needed
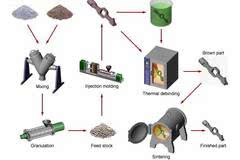
blend
Fine metal powder and thermoplastic, paraffin binder mixed in a precise proportion. The mixing process is carried out in a special mixing equipment and heated to a certain temperature to melt the binder. Most of the particles are mechanically mixed until the metal powders are uniformly coated with binders and cooled to form granules (called raw materials) which can be injected into the mold cavity.
Forming
Injection molding equipment and technology are similar to injection molding. The granular material is fed into the machine and heated into the mold cavity under high pressure. This link formation (green part) and demoulding after cooling, only in the condition of C about 200 degrees to the adhesive to melt (fully integrated with metal powder), the whole process can be carried out, the mold can be designed as a multi cavity to improve productivity. The shrinkage in the sintering process of metal parts should be considered in the design of cavity dimensions. The shrinkage variation of each material is accurate and known.
Skim
Degreasing is the process of removing binder from molding parts. This process is usually accomplished in several steps. Most of the binders are removed before sintering, and the remaining part can support the components into the sintering furnace.
Degreasing can be done in a variety of ways, the most commonly used solvent extraction method. The components after degreasing are semi permeable, and the residual binders are easily volatilized during sintering.
Sinter
The degreasing parts are placed in a furnace controlled by high temperature and high pressure. The component is slowly heated under the protection of the gas to remove the residual adhesive. After the binder has been completely removed, the component will be heated to a very high temperature. The voids between the particles will disappear because of the fusion of particles. The component is contracted to its design size and converted to a dense solid. For most of the materials, the typical sintering density is theoretically larger than 97%. High heat density makes product performance similar to forging material.
surface treatment
According to the specific requirements, some components may need surface treatment after sintering. Heat treatment can improve the physical properties of metals. Electroplating and painting can be applied to high-density materials. Providing welding or cooling treatment techniques.
Process video display:
3, MIM products usually have the following characteristics
complexity
MIM, like injection molding, has no limits on shape design. Since MIM is a molding process, additional product features do not increase cost, which makes MIM an ideal way to combine independent components into multi-functional products. MIM design rules are very close to injection molding, and are applicable to almost all products.
Precision
The reference design of MIM net forming accuracy is usually the size of + 0.5%. The net forming energy of some properties is up to + 0.3%. As with other technologies, the higher the accuracy requirements, the higher the cost, therefore, in the quality permit, encourage the relaxation of tolerance requirements. MIM can not be achieved by one time molding can be achieved by surface treatment.
Weight and size
MIM is particularly suitable for parts weighing less than 100 grams, less than 50 grams is the most economical. However, the weight of 250 grams of components can also be dealt with. The main cost of MIM process is raw material, so MIM uses new technology to reduce the weight of parts as much as possible. Like plastic products, the weight of the parts can be reduced by the core and the bracket without affecting the integrity of the product. MIM is outstanding in micro and micro parts, and weighs less than 0.1 grams is also feasible. Weight is not a limiting factor. Products with a length of more than 250mm can also be processed.
Low Profile Power Inductor
Wall thickness less than 6 mm is the most suitable for MIM. Thicker outer walls are also possible, but the cost increases due to long processing time and additional materials. In addition, the extremely thin wall below 0.5 mm is also able to achieve MIM, but the design has a high demand
yield
MIM is a flexible process, and the output of several thousand to several million dollars per year can be realized economically. Like castings and injection molded parts, MIM requires customers to invest in tooling and tooling costs, so for small quantities of products, it usually affects cost estimates.
raw material
MIM can deal with many materials, including ferroalloys, super alloys, titanium alloys, copper alloys, refractory metals, hard alloys, ceramics and metal matrix composites. Although nonferrous alloys, aluminum and copper, are technically feasible, they are usually handled in other more economical ways, such as die casting or machining.
4 、 MIM design guidance
MIM is widely applied to various automobiles, electronics, medical, industrial, consumer products and other industries, including auto parts, aerospace equipment, mobile phones, dental instruments, electronic radiator and seal packaging, electronic connector hardware, industrial tools, optical fiber connector, spray system, disk drives, medical equipment, electric tools, surgical instruments and sports equipment etc..